Welcome back to Cnuteneering, where the possible is made more difficult by bone headed ignorance, overenthusiasm and pointy metal things being brought together.
You may want to refresh your memory on the project in:
Design goals:
Fast as possible on offroad; too big to have on roads. I will set a target speed of 50mph.
4 WD.
Must be able to reverse, and brake.
Unbreakable, or as close to.
Must be able to mount GoPro or similar camera on it.
Cheap as possible.
We left the last episode of Cnuteneering with a shiny new gear changer. Some measurements were taken of RPM counts on key parts of the gearbox and found to be largely in line with modelled values, or at least close enough for Cnuteneering.
What I really need though is to get the TelePi fitted and start getting some actual in-use data. Avid readers will recall that the TelePi records GPS latitude, longtitude, speed, engine temperature and 3 RPM counts.
The RPM counts will ideally be the engine output, and then either side of the main central diff to record the RPM of the front and rear driveshafts that feed into the front and rear differentials. Looking at the gearbox though there is no way to mount the RPM counter so it can directly read the main pinion gear, the next gear along is a possibility though.
Luckily, last time I had the gearbox apart I put some holes in where I thought the RPM counter would be mounted, so a bit of polycarbonate spacer to be inserted and I am good to go. The Forward Planning Committee takes a bow on this one.
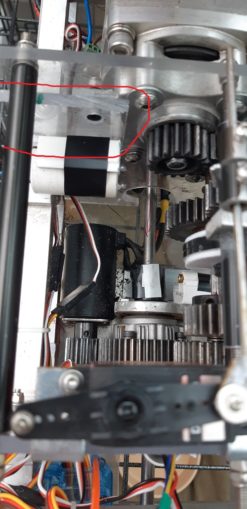
Firstly, I fit the front sensor. The plastic conduit grips the RPM counter housing so it should be quite easy to remove when I am just mucking about driving for fun, rather than using the TelePi to collect data.

Next I fit the rear diff drive and second-gear-after-motor RPM counter.
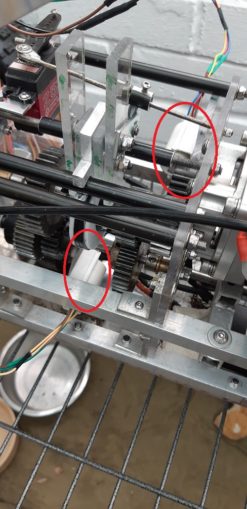
There is a handy threaded M4 hole on the side of the engine block that will be useful to mount the temperature sensor on. So I carefully drill out the mounting plate on the temp sensor.
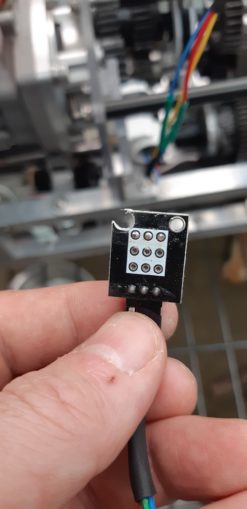
Not carefully enough it would seem. I have some heatsink glue though so I prop it up against the bottom of the crank case. There is no real way of attaching it to the engine cylinder which would give a better idea of how hot the engine really is, but it’ll do as a proxy for now. The main engine block has cooling fins which would be very hard to attach to.
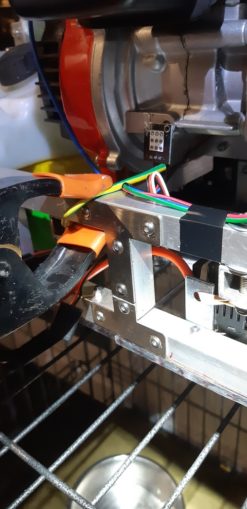
Now that all the sensors are in the right place, I use insulating tape to hold the cables tidy. There. Must. Be. Order. Ish.
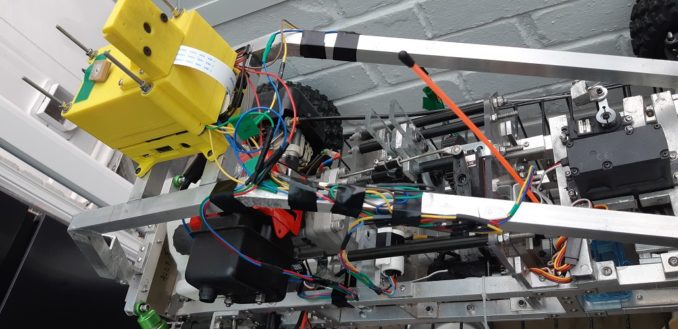
Not quite as tidy as I’d like but these cables could go in some sort of thin plastic trunking when it is all done, or I can just leave them as is. The Cnutmobile does look like it should be in hospital though, with all these wires snaking about all over it.
Now to power on the TelePi and check aim.
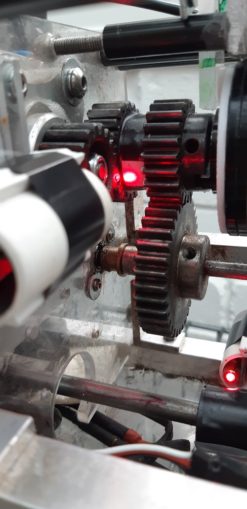
As I am fussing about with the RPM sensors, I see that they have a tendency to spin in the trunking housing that is attached to the body. A little bit of black insulating tape holds them properly in place but still easily removeable.
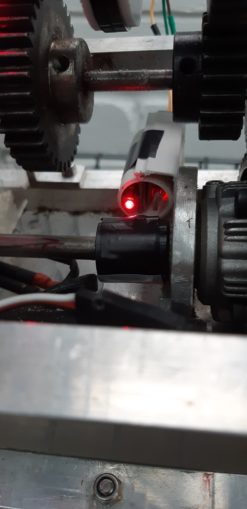
It does look quite impressive at night I think.
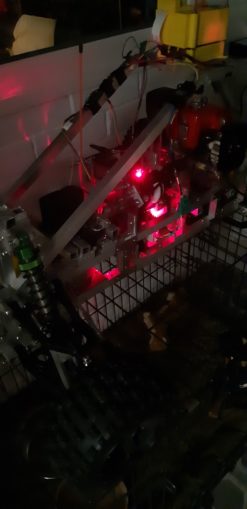
Before taking it out for a run, I think about putting the swanky new air filter on. The new air filter is much better looking, and crucially, will provide a nice round interface to accept the output from the supercharger, if I ever get around to building it, or an inlet for the Nitrous Oxide feed.
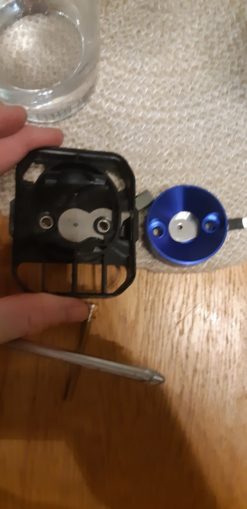
However the supplied bolts are not long enough and I appear to have a local shortage of M5 bolts that are long enough. Call the press, there are no M5x60mm bolts in SE London!
I can now test that all the sensors are working by plugging the Pi in to a static power cable, and using a little test program I wrote to read the RPM sensors. Miraculously, they all seem to work still, when I flash a bit of reflective material across their fronts.
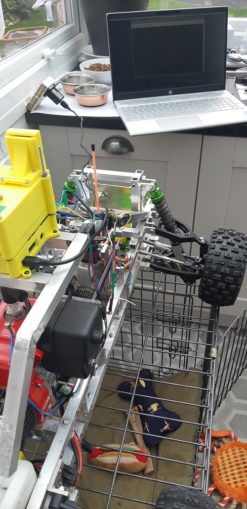
The conservatory seems to look more like an F1 garage now, with cars and laptops everywhere.
So now I bundle everything up into my car, offer a silent prayer to the Gods of Cnuteneering and drive to my test site.
The dead end road appears to be fully loaded with tens of Uber cars which is annoying as an on road test drive would be ideal right now. If anything else falls off the car it’d be a damn sight easier to find the parts that fell off on tarmac than in grass. Never mind, part of Cnuteneering is adapt, overcome and let no one see you cry.
I enable mobile tethering on my phone, and fire up the TelePi. The Raspberry Pi has a WiFi connection configured so it uses my phone to manage the network. This means I can run a remote desktop from my phone to connect to the TelePi, and start the recording process.
Quivering with antici-pation, I begin the run:
Top speed looks like 28kph in 1st gear which sits just about inside my models for speed. The brakes seem to be having a minor effect at best, which is a worry. The data captured seems to be a bit off; poor source control and release management to the unit a few months ago meant I had old software on there that calculates in KPH and puts too much clutter on the video output. I have now rectified this.
I try to engage 2nd gear and manage it quite nicely (not shown in video) but I am concerned that the brakes are not really up to much and there are people moving about in the distance, so I don’t go full on crazy with it. I will need to either find somewhere a bit more secluded or address the lack of brakes sooner than I’d like. I was not as clinical in my testing of 2nd gear either, mostly concentrating on getting 1st gear tested before anything broke or fell off. I was largely enjoying driving the car, to be honest.
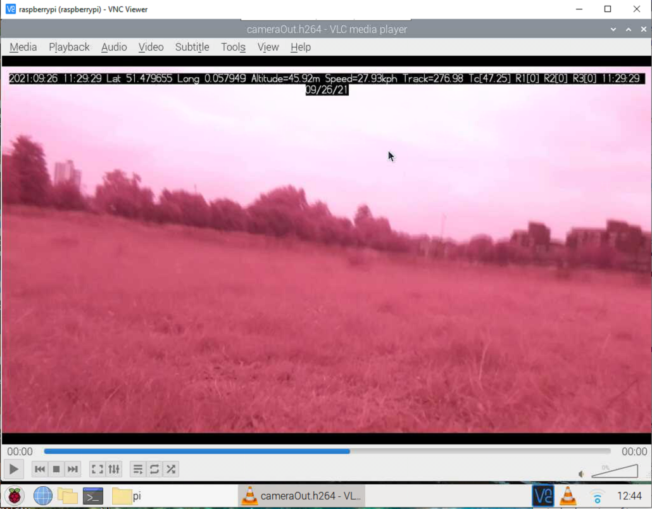
The video looks like it was taken on Mars because I am using the IR camera from the El Cnutador’s ARSE project as there was no budget to get a new camera for the project, once I had finished fitting out my luxury purpose built workshop and funding a team of designers to add things to fall off the car. I also need to properly calibrate the RPM counters as they are seemingly not noticing that there is rotational activity in front of them. I am not sure how to do that easily as the sensor test I have needs the reflective strip to be in motion which is hard indoors, but it is something to think about.
I think the problem is the angle of incidence needs looking at – the laser pointer reflection is bouncing off the reflector away from where the sensor can see it.
On returning home, I set the pi back up on the home network and begin pulling the 1.1Gb file of data off, to edit down and view. And then it is time for the butcher’s bill.
As I was mucking about with the gear changing I was not really paying attention to the rotation of the control knob that moves the gear changer and predictably, the friction was too much.
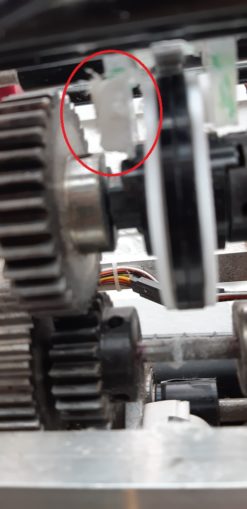
In the above you can see where the PTFE button guide has completely worn away, and then began eating the polycarbonate.
This is looking pretty knackered when I remove the assembly from the car.
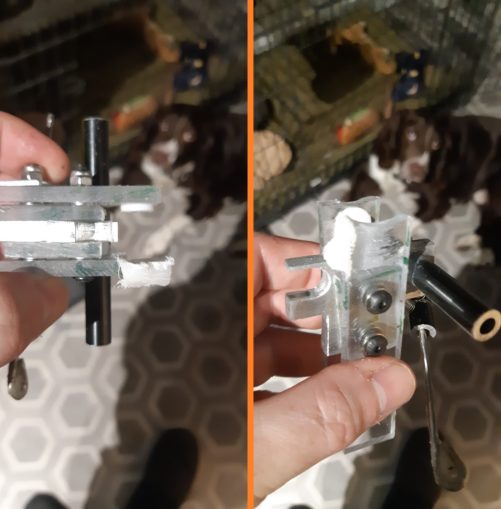
You can really see the damage on this close up – in the green circle there is the 2nd gear tine and in the red, the 1st gear tine. The polycarbonate has melted and wrapped backwards over itself. I really need to sort out the end point adjustments on the servo, or at least go a bit easier on the control knob instead of just “full on”. But it is so much fun to drive!
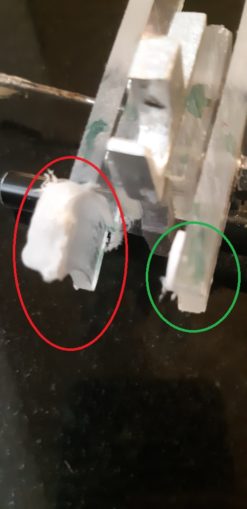
The handling of the car was quite nice though, the four wheel drive seems to grip the road and grass quite well, and it is reassuringly tail happy as I go around corners. I have not really given it full beans from a standing start as yet because I think that is going to be the driving that breaks stuff. I will have to do that, but for now I am just enjoying having a car to play with. The front steering servo might need some beefing up as the servo does wobble a little at low speeds. I can take another look at that and see if it is struggling at full speed or not.
On the plus side, I fixed the gear changer with a minimum of fuss. Just need to think about calibrating the RPM counters, sorting out the braking mechanism and and and and and…
In the meantime, though, there are far more important things to play with.
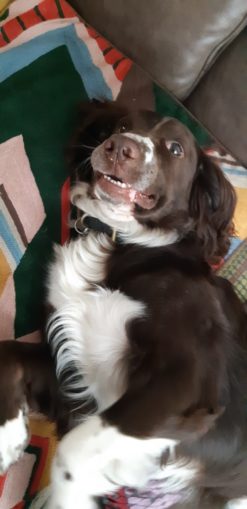
Still waiting for:
Nothing!
Still left to do / think about
End point adjustment for servos and control mechanisms Dumbo RC setup
Sort out some actual working brakes
Write telemetry data out to a file instead of just to screen / video output
Calibrate RPM counters so they actually work
Body shell
Pics, vids, words and music © El Cnutador 2021