Welcome back to Cnuteneering, where the possible is made more difficult by bone headed ignorance, overenthusiasm and pointy metal things being brought together.
It’s been a while – you may want to refresh your memory on the project in:
Design goals:
Fast as possible on offroad; too big to have on roads. I will set a target speed of 50mph.
4 WD.
Must be able to reverse, and brake.
Unbreakable, or as close to.
Must be able to mount GoPro or similar camera on it.
Cheap as possible.
We left the last episode of Cnuteneering with an update from before Christmas and a little easing back into things. The CheatMobile has made an entrance although has failed to live up to expectation, the 4wd kit installation was a bit longer than I expected, and there is a problem in the transmission to the rear axles.
No matter, you are here for the Cnuteneering, the highs and lows of trying to do some actual engineering with no proper tools, no formal training and no bloody clue.
Firstly the chewed knuckle needs looking at.
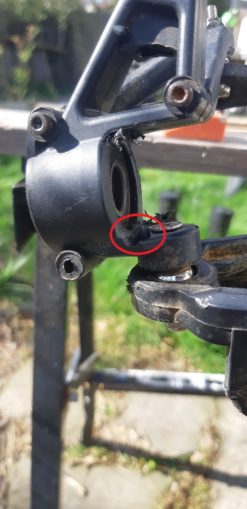
This was due to the cotter pin in the CV driveshaft coming loose, and smashing against the plastic. I have fixed this with my old friend, JB Weld, and re-fitted it to the car. I also took the opportunity to rotate the wheels from the CheatMobile to the CnutMobile and vice versa, the CheatMobile’s stock tyres are more for road use.
That is about all the mechanical repairs that needs to be done; however I have not yet fired up the engine so I am hoping the 6 months of storage haven’t done any damage.
There is of course, the obligatory Tennis Ball Time that needs to be delivered. Doggie Walks Matter!
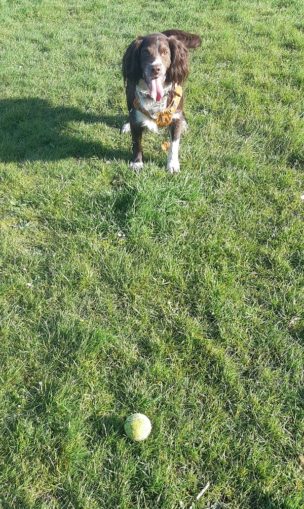
Next up is to sort out the TelePi properly. It was built in a bit of a mad scramble just to get some telemetry and video but it now needs attention.
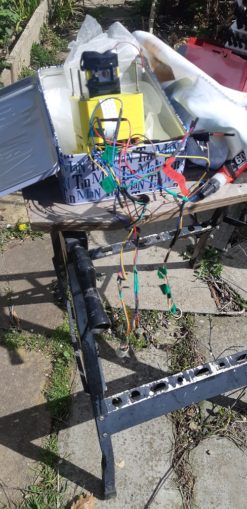
Puffins will recall that the TelePi suffered from my unfamiliarity with the ABS plastic I used to get the case 3d printed – the legs I had designed were in no way sturdy enough to take the vibration and shocks and have pretty much all broken.
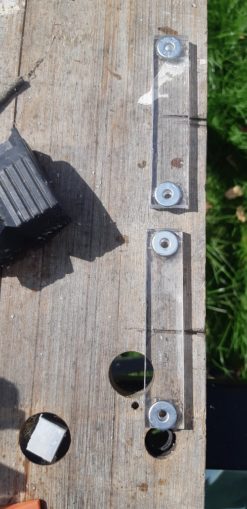
I cut some polycarbonate to size, and superglue some washers to them for extra sturdiness.

And then glue them in place, with a helpful heavy object on top to keep the plastic nicely compressed together.
Next up is the piece I am most ashamed of, the bought-in brakes. I take a quick look at how they are to fix to the rear wheels and am secretly delighted that I don’t need to drill, tap, cut, glue, weld or otherwise bodge anything to put them in. I do need to work out how the pull mechanism is going to work though.
I may have to relax the “must be reversible” design goal in order to fit them in. The electric motor is not quite up to the job of braking the car, and reverse may be a luxury I will have to do without.
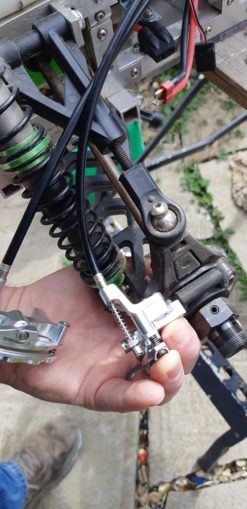
On the plus side there is always some dogtime to take the mind off things
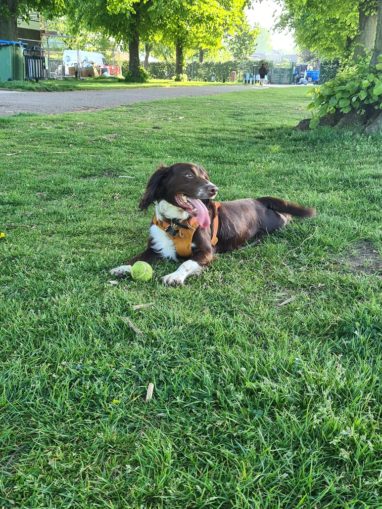
With the TelePi now with stronger lugs mounted, I fix something that has been bothering me for some time, the IR filter over the camera was just taped on to see if it would work. I remove the tape and do it properly. I have to file out a little of the edges on the lense so I can get the mounting screws in, but at last it is done.
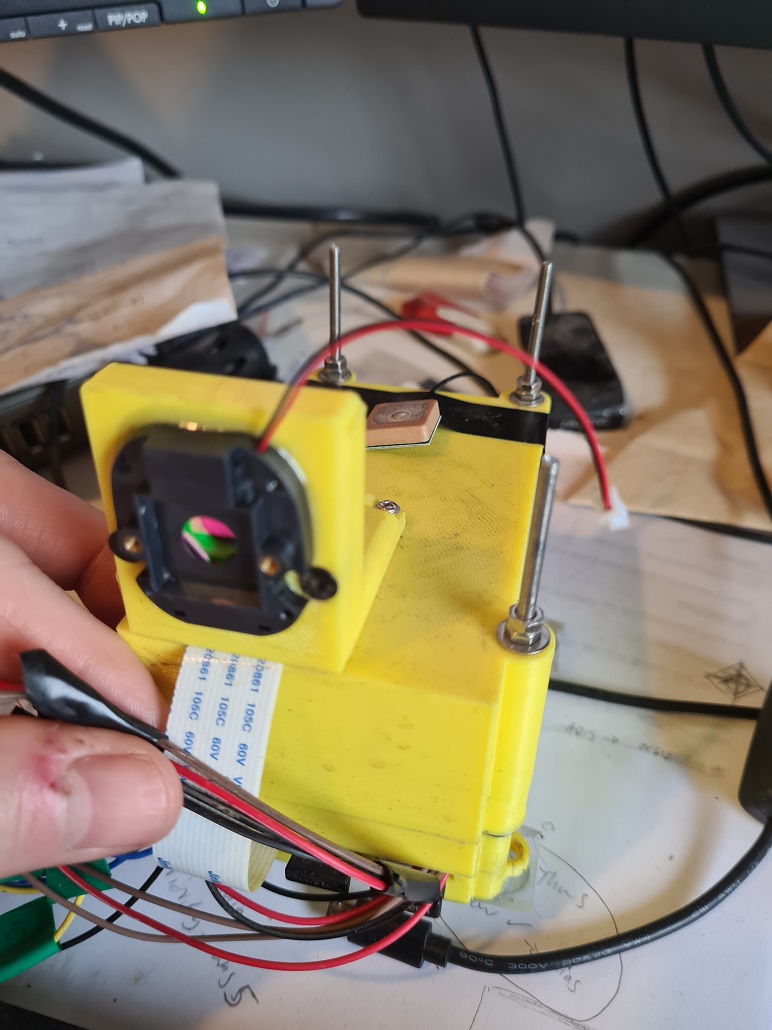
Now I am nearly ready to begin the last part of re-assembly, and attach the TelePi back to the Cnutmobile.
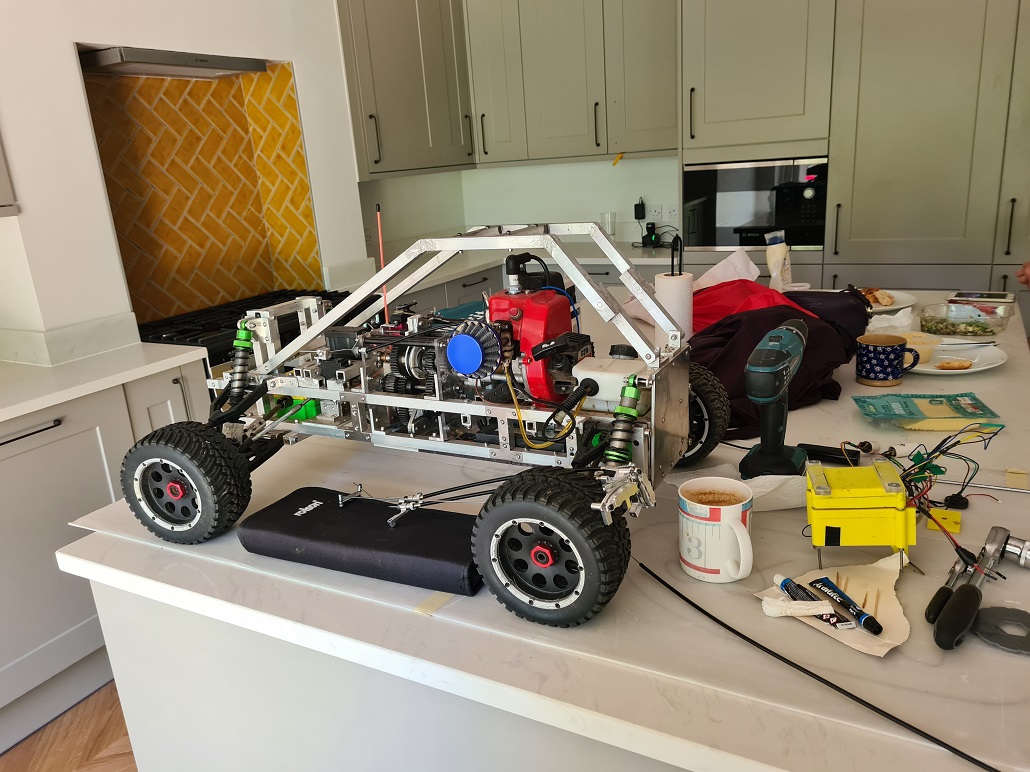
The garagelab is still under construction so I make do in the kitchen. There is horror from MBWK.
Next up, I really need to get the RPM sensors properly aligned. I cannibalise some old code and repurpose it.

I also waste a few hours wondering why all the spanky ncurses stuff I added to make readout of sensor values easier seemed to have no effect; turns out in Visual Studio their shell emulation is crap. The new code will allow me to position the sensor right over the reflector, and hopefully start getting more reliable readings when I finally take the Cnutmobile out after its long holiday.
If I no longer need the electric motor, I will no longer need the ESC (Electronic Speed Controller for the brushless motor) that drives it. This is going to be a problem as the ESC also provides an inbuilt UBEC (Universal Battery Eliminator Circuit) which converts the 11.1v from the battery to 5v to power the servos and radio receiver. Going to have to have a think about this one I reckon, it is a pretty large design decision and goes against the original design plan. I think a 5A with a 7.5A peak should do it, something like this.
On the plus side, the new pillar drill has arrived.
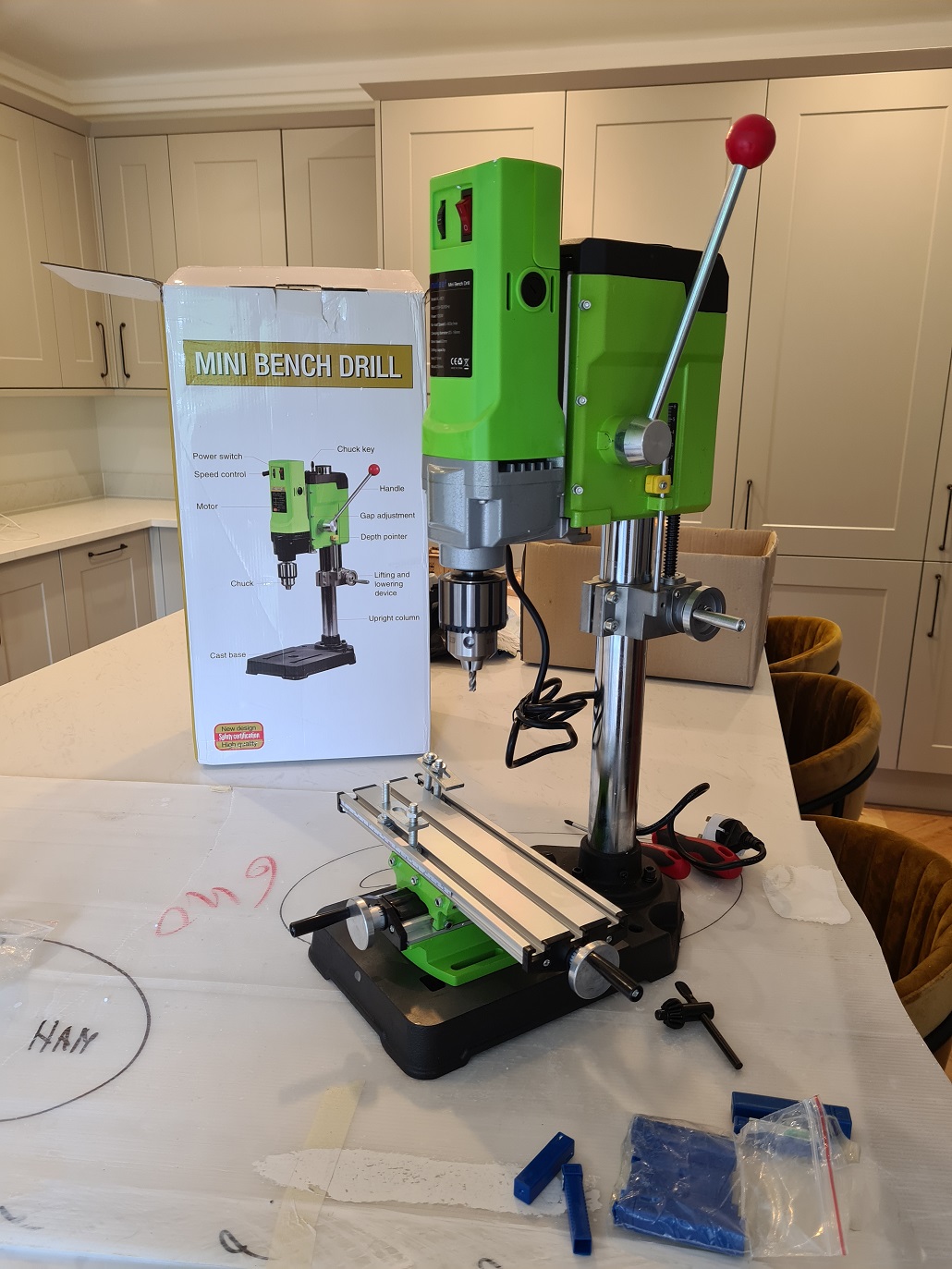
An attempt at milling into a bit of aluminium box is not as clean as I’d like. The drill head has too much travel in it, as the drill column mounts to the stand there is just a little bit of play in there. I am hoping I can tighten this up at a later date.
As it is, I can mill – just about. The milling table is just about strong enough to move the material into the cutting head, but as you can see, it is not a nice clean line that is cut.
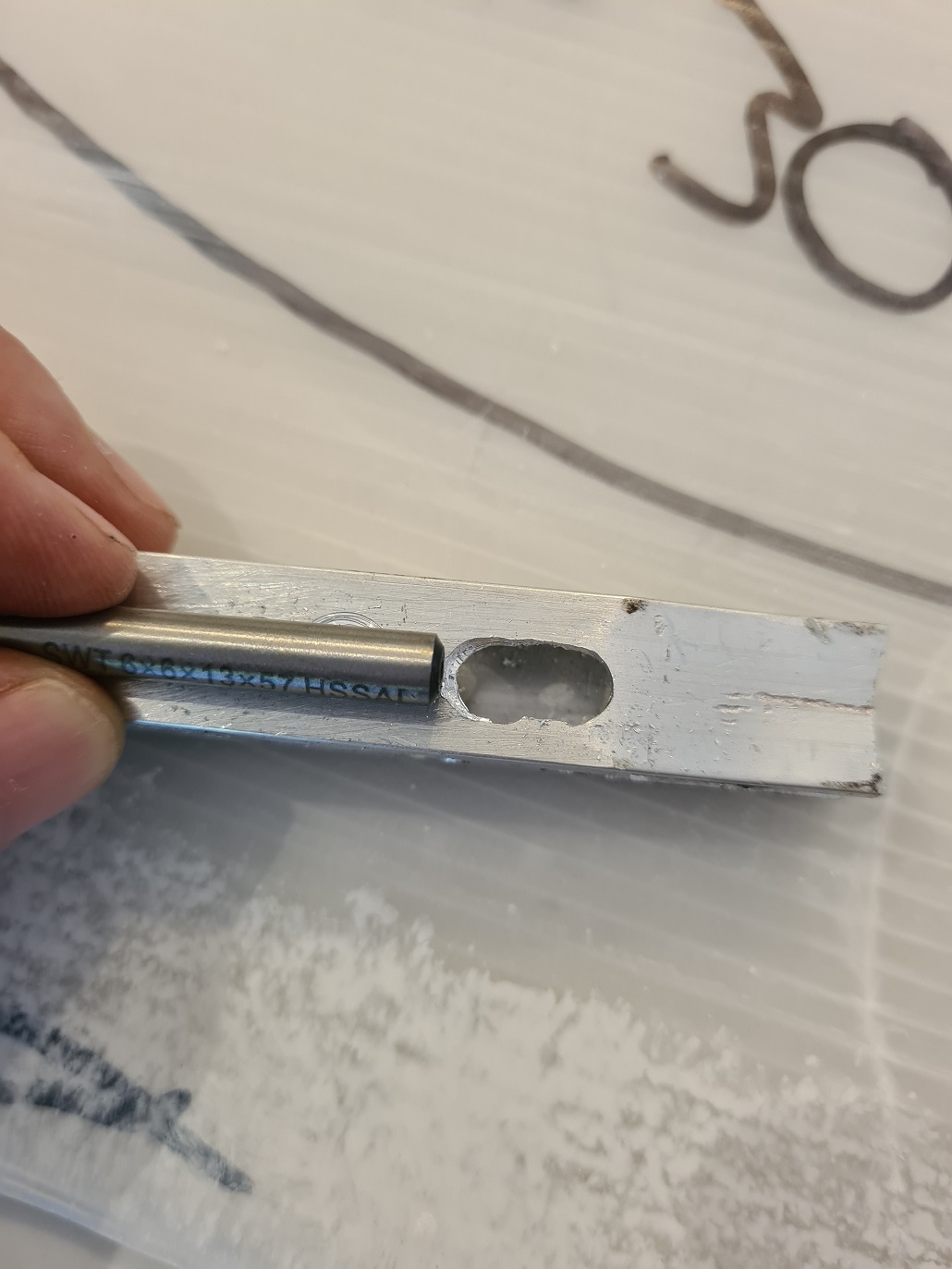
The milling table is a bit crap as well, I got some swarf trapped in the threads of the movement and so had to disassemble the thing to clean it all out.
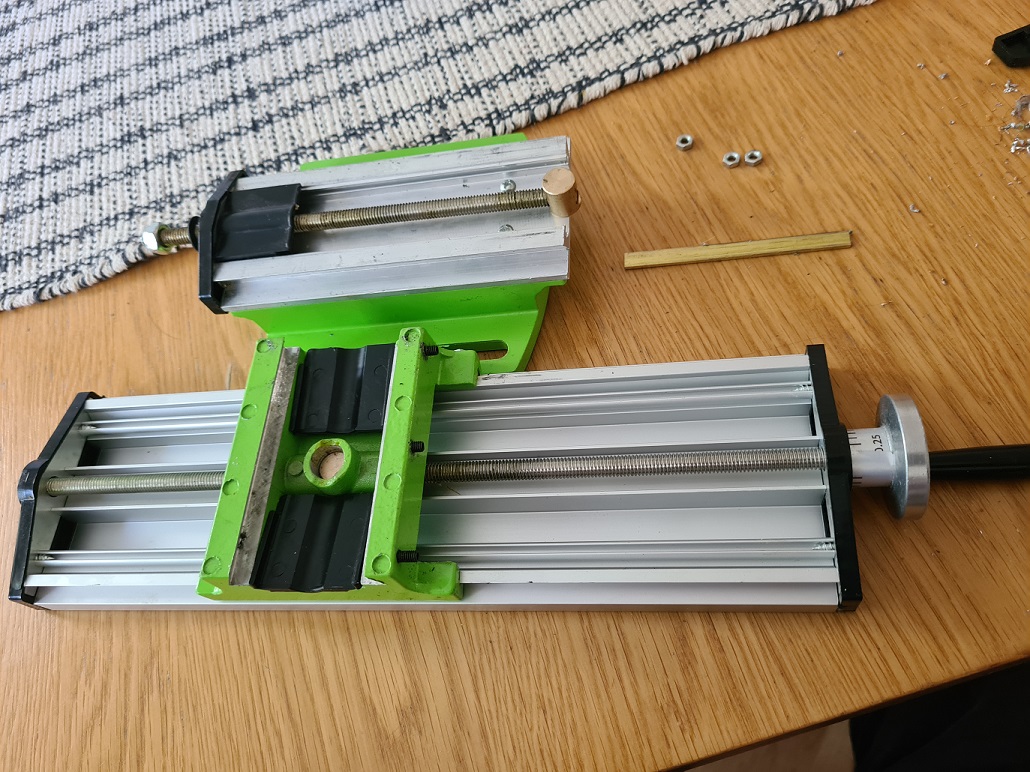
In the meantime however, there is this to consider for the CnutMobile mark II.
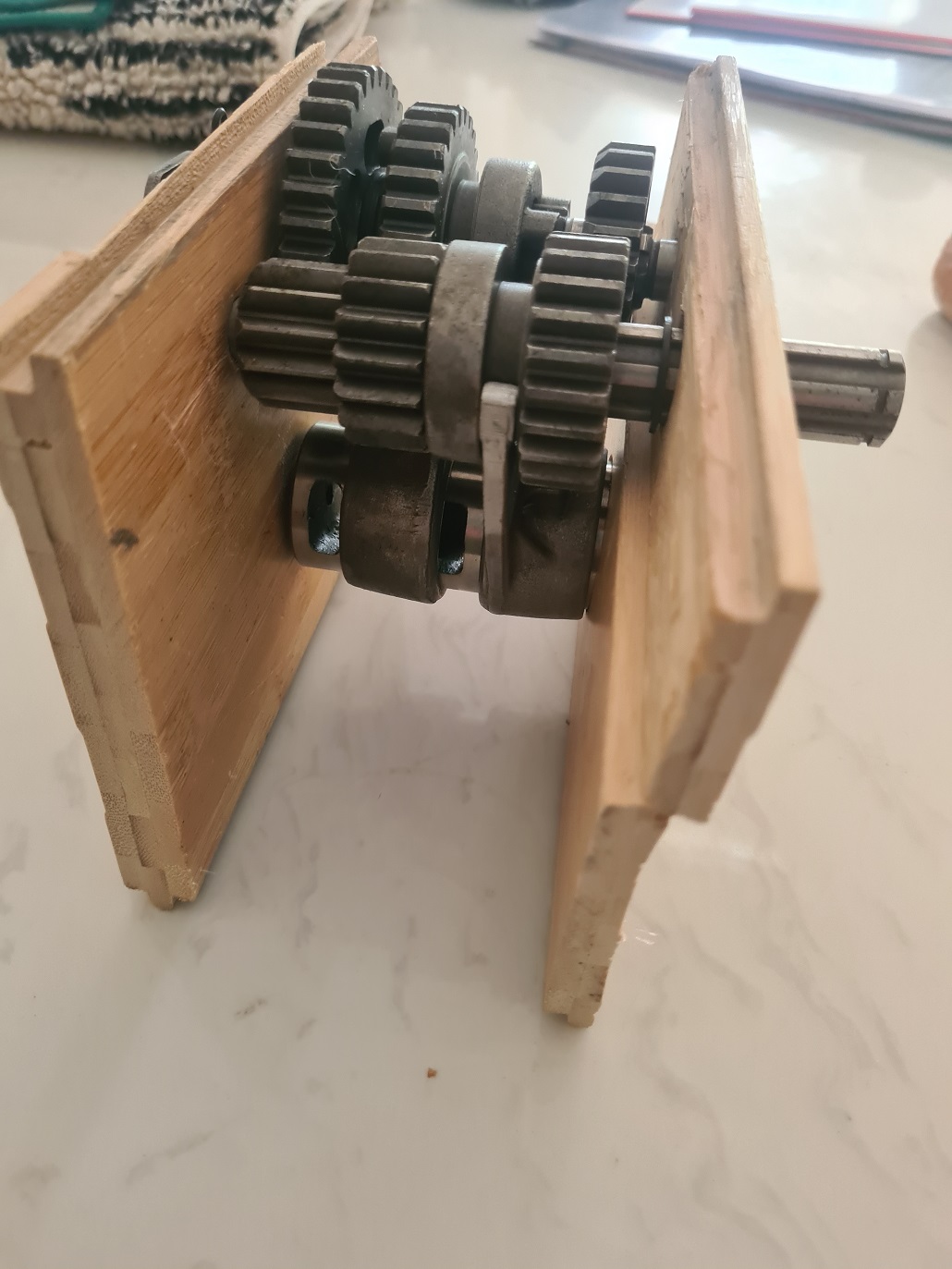
Still waiting for:
Nothing
Still left to do / think about
Sort out sensor aim
End point adjustment for servos and control mechanisms Dumbo RC setup
Body shell
Affix fuel tank so it does not bounce about
Move gearchanger to 3 position switch on Tx
Move electric motor off throttle channel
Look at how Root superchargers work
Pics, vids, words and music © El Cnutador 2022
The Goodnight Vienna Audio file
Audio Player