We’ve already explored the development of the Periodic Table (a.k.a. the Periodic Table of the Elements) and picked up a few bits of basic chemistry information. The elements we have met to date have been: Hydrogen, Carbon, Mercury, Bromine, Oxygen, Iron, and Sodium.
This time, we’re going to have a look at another of the transition metals. It’s an element I’m really rather fond of, not least because it is only one of two elements after which an ‘Age’ is named. Iron, which we covered in a previous piece, being the other.
This episode will tell Copper’s tale. It’s not exactly something that could be considered a precious metal, but it is an attractive one, and an eminently useful one too.
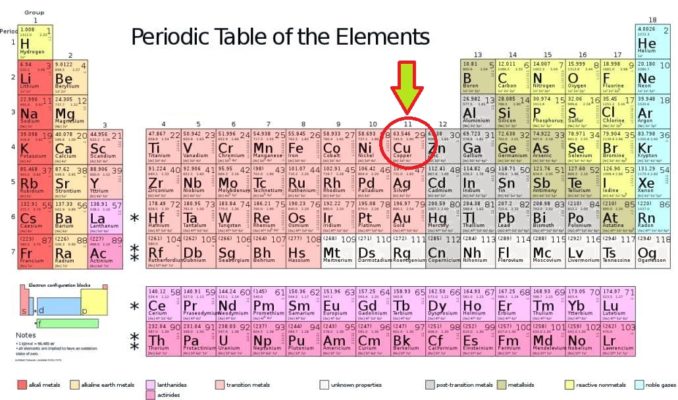
Modified from 2012rc, licensed under CC BY 3.0
Copper, which has been assigned the symbol Cu, is the 29th element of the periodic table. It is the first of the elements in Group 11. As well as copper (Cu), Group 11 includes silver (Ag), gold (Au) and the radioactive roentgenium (Rg). This group is sometimes referred to as the ‘coinage group’ as coins have been minted from copper, silver and gold or their alloys.
Copper is one of the transition metals, otherwise known as the d-block elements. As we saw with iron, these are elements which, because of the way in which their electrons are arranged, can take part in chemical bonding using electrons, not just from the outermost shell (the usual state of affairs). They can also donate an additional electron from the next electron shell.
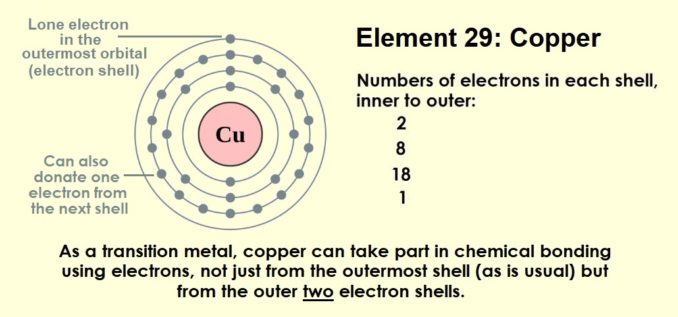
SharpieType301, 2023
For copper, this means that, in compounds, it can have an oxidation state of either +1 or +2 (remember, any electrons it donates leads to it acquiring a positive charge). Therefore, its ions can be either Cu+, by donating an electron from its 4s orbital, or Cu2+, by donating an electron from its 4s orbital and an electron from the 3d orbital. Interestingly, one way to distinguish the two is by using colour, or rather their emission spectra. When heated in a flame, copper(I) produces a blue flame, whereas the flame from copper(II) is green.
Untarnished copper has a characteristic soft pinky-orange hue. This makes it one of only four metals whose colour is not silvery or grey, the others being gold (whose colour needs no explanation), the blueish-white osmium, and caesium which is a rather Tolkein-esque silvery-golden metal.
As a metal, copper is relatively soft. It is malleable (easily shaped or formed by hammering), and ductile (easily drawn or stretched into wire). Copper has very high thermal and electrical conductivity (in both cases, second only to silver amongst the metals).
It has a face-centred cubic crystal structure, with no allotropes. In total, copper has twenty-nine isotopes. Of these, only two, 63Cu and 65Cu, are stable, with 63Cu being the most abundant.
Some of copper’s radioisotopes have found uses in medicine, with 67Cu and 64Cu used in the radiotherapy component of some cancer treatments to destroy or curb the replication of malignant cells. Other radioisotopes are used diagnostically, as radioactive markers in medical imaging, especially positron emission tomography (PET). They are useful tools for research as the chemistry of copper and its role in biology is well understood. Furthermore, the radioisotopes can be linked to a range of peptides, proteins, antibodies, and other small organic molecules.
Copper is one of only a handful of metals that occurs as a ‘native’ metal, that is as an element (in a relatively pure form) in nature which can be picked up and used without any particular processing. This had implications for its use in antiquity, as we will see.
Because it can be found in its native form, copper as an element, similarly to iron, wasn’t ‘discovered’ per se. This metal has been exploited for a very long time. Native copper’s malleability allowed it to be fashioned relatively easily into ornaments and jewellery (e.g. rings, earrings, bracelets and beads), but also into tools, and weaponry (e.g. daggers, arrowheads, and awls, since it can hold a sharp edge, at least for a while). Metal tools and weapons took off because copper can be worked much more easily than the stone which preceded it.
Worked copper is seen much earlier than iron, where the oldest known use comes from meteoric iron used to produce beads, dated to c. 3,300 BC. In contrast, there’s some evidence for copper, as far as c. 9,000 BC, being ‘cold worked’ into small items such as awls, beads, discs, hooks, and reamers at Çayönü Tepesi, a Neolithic settlement at the foot of the Taurus mountains in Turkey.
Other early ‘cold worked’ examples include a pierced lenticular copper pendant (heavily mineralised) excavated in the 1950s by by Rose and Ralph Solecki at Shanidar in northern Iraq, dating to c. 8,700 BC. A number of copper beads have been excavated at Anatolian sites: a single bead was recovered from Nevalı Çori, dated to 8,200 BC, and other beads were found at Çatalhöyük, dating to around 7,500 BC.
The next development in the history of this metal’s use is likely to have been annealing (a deliberate heat treatment). Annealing copper at 500° C (above the metal’s recrystallisation temperature), followed by carefully controlled cooling, releases strains in the metal’s microstructure caused by defects and imperfections in the grains (crystals). As the grains reform upon cooling, they do so more perfectly. This makes the copper more workable, as the process changes both the structure and physical properties of the metal to reduce its hardness and increase its ductility.
Although exact dates for this technological discovery are a little hazy, to say the least, it may well be that this was a relatively early process, possibly even mirroring the dates we have already seen. After all, heating materials to modify them was not new: heating flint to improve its quality for knapping had long been known.
Even in the New World, evidence of mining and annealing native copper, is thought to date back to c.5,000 BC. At the start of the Old Copper Complex of the Western Great Lakes, native copper nuggets found in gravel beds from glacial drift were used. But, before long, copper was being quarried by the Native Americans. Hundreds of pits and trenches were dug on Lake Superior’s Isle Royale, and readily available deposits were exploited and traded from the surface rock and shallow diggings on the Keweenaw Peninsula in the Upper Peninsula of Michigan at the south shore of Lake Superior. In all, tens of thousands of artefacts have been found.
The native copper found here is remarkably pure, usually over 95% Cu. Interestingly, the Keweenaw Peninsula is the location where the largest single mass of native (elemental) copper has ever been unearthed. Found in 1857, this was one humongous chunk, weighing in at some 463 tons.
The next big step was smelting, that is the process of heating copper ore (initially carbonate ores) to extract the metal. This took a little longer to be realised. Most archaeologists agree that there were multiple points of origin for copper smelting. However, by c.5,500 to 5,000 BC, evidence of copper smelting is seen at sites in Serbia, including Belovode and Pločnik. Slightly later, around 5,000 to 4,800 BC, copper smelting took place at Sitagroi (northern Greece), Dikili Tash (eastern Macedonia), Usoe (Bulgaria), and Anza (the former Socialist Republic of Macedonia, part of Yugoslavia).
There is no doubt that the use of and technologies relating to copper spread far and wide. A valuable resource, it was traded extensively. A good example comes from Ötzi, the naturally mummified, frozen remains of a gentleman discovered high in the Ötztal Alps (on the borders of Austria and Italy) in 1991. His body has not been dated precisely, but he’s thought to have lived at some point in the period from 3,350 to 3,105 BC.
Ötzi, nicknamed ‘the Iceman’, carried a hand axe, carefully crafted with a cast copper head, secured to a yew wood handle with hide strips, and birch tar. Yeah, so what, one might say, there are deposits of copper in the Alpine region, and this was known to be exploited in Ötzi’s time.
But painstaking analysis from a tiny chip of the metal reveals that the copper comes not from nearby, but from southern Tuscany, some 350 miles from where Ötzi drew his last breath.
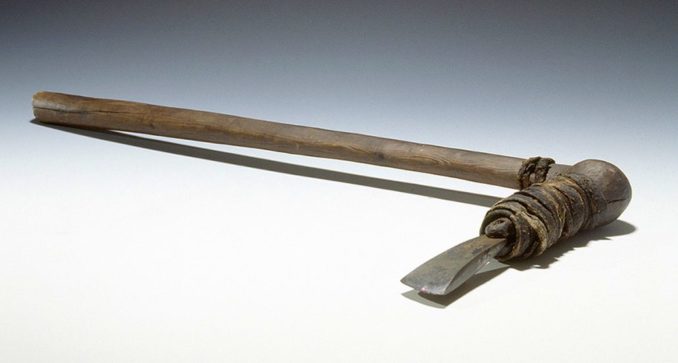
VitAntica, licensed under CC BY-SA 4.0
This is perhaps surprising, but it raises a few more questions. Could the ores to produce this axe have been traded over that distance? In my view is this is unlikely, especially given the constraints of transporting weighty ores and proximity of local copper ores. Alternatively, was the raw metal traded, or was the axe head made in Tuscany and traded?
We don’t know for certain, though some have suggested a clue may come from analysis of Ötzi’s hair. This showed high levels of copper particles and arsenic so, in theory, might mean that Ötzi had smelted the raw materials to produce copper himself. Thus, it is possible that he made his own axe head from ore traded north. I must admit that my money would not be on the metal ores making the trip, so if he were involved in copper smelting, it isn’t likely that this was to produce his axe head. Go on, change my mind.
As production of copper through smelting, primarily to make tools, armour, and weaponry, stepped up, and wide-spread manufacturing intensified, the ‘Copper Age’ (also called the Chalcolithic period) began. This marks a period of massive transition, between the early settled agrarian cultures of the late Neolithic, and the increasingly urbanised, autonomous, and independent city-state societies of the Bronze Age with their painted ceramics, rise of socio-economic differentiation, and emerging literacy.
Throughout history, copper’s importance has never waned, even with the coming of the Bronze Age (which relied upon the element) and the Iron Age. In fact, it retains its importance to this day, as we will see a little later.
Copper can be found amongst the alchemists’ ‘seven metals of antiquity’, and it was the Ancient Greeks and Egyptians who first used the symbol we see below (the ankh, ☥ which symbolises ‘life’ and ‘immortality’) with which we are familiar.
In Egypt, our metal was closely associated with Osiris (son of Ra, and god of the underworld), who was often depicted with green skin. It was Osiris who introduced the Egyptian people to copper implements. Incidentally, that green pigment, known as ‘eternal green’ or wahdj, was a precious colour to the Egyptians (signifying life, and verdant vegetation, but also death and the afterlife).
Where did their rich green pigmentation come from? It’s made from the mineral malachite, Cu2(CO3)(OH2) or copper carbonate which, finely ground, they used as a pigment, and in cosmetics. They also used malachite as a semiprecious gem, often carved, in statuary, and in jewellery (it symbolises protection from evil).
The Egyptians also made good use of another highly prized copper-rich mineral. Used in pigments and as a semiprecious stone, this is the beautiful bluish green turquoise, to the Egyptians, mefkhat. Turquoise is a hydrous phosphate of copper and aluminium (CuAl6(PO4)4(OH)8·4H2O). Again, this stone was associated with fertility and vegetation.
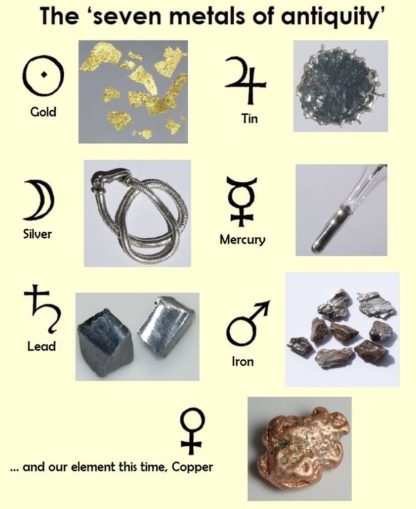
SharpieType301, 2023, images from Chemical Elements, licensed under CC BY 3.0
The Romans then used this same symbol, but linked copper with Venus, their goddess of love and beauty. Copper was given this association for the attractive appearance of the metal itself, and also because, highly polished, it was used to make mirrors, reflecting the ‘beauty’ of the holder.
As you can see above, the modified ‘ankh’ symbol used for copper (and the planet Venus) remains familiar to us. It’s the one Swedish botanist Carl Linnaeus chose to denote a biologically female organism (you might remember that, to convey male, he used the ideogram for Mars). I am all too aware that it’s been a little overshadowed by the LGBTXYZ?! alphabet expansion these days, but it remains valid.
Our name for this metal, ‘copper’ (with a first known usage c.1530), comes from the Old English word ‘coper‘. I find it quite interesting that this same word, in the term ‘horse coper’ was also in use, by around 1615, to describe a horse dealer, usually a somewhat disreputable or untrustworthy one. I haven’t been able to find concrete evidence, but I suspect this somehow relates to the use of copper as coinage. However, ‘coper‘ in terms of our metal, stems from an older, Proto-Germanic word ‘kupar’, which itself derives from the Latin ‘cuprum’ (from where we get the elemental symbol Cu).
It is this Latin word which explains better why our element copper was given the name we use today. During the heyday of the Roman empire (31 BC to AD 476), their main source of copper was the sulphide ores from mines in the foothills of the Troodos mountains on the island of Cyprus. Thus, the metal became known as ‘aes cyprium’ (metal of Cyprus). Since this is a little clumsy in general conversation, it gradually morphed into ‘cuprum’.
That said, the copper resources on the island had been in use well before Roman times. Cyprus has been inhabited since the Neolithic, c.8,800–8,600 BC, when the first agriculturalists settled on the island. The first metalwork (copper, of course, used to make tools) dates to 3,500 BC, and it is likely that this is when the name Kúpros, which is what Cyprus was known as in Ancient Greek, dates to.
Copper and its ores were more easily collected from surface deposits at this point. Thus again, the Greek name is one which can be directly linked to our element, doubtless reflecting this valuable, and tradable, resource.
We’ve mentioned that Cyprus was rich in sulphide ores, but quite a number of copper ores are mined to produce this metal. They fall into two rough groupings: oxide ores (copper chemically combined with oxygen) which are found in the upper ore deposits, and sulphide ores (copper with sulphur) from the lower levels.
The ores can vary quite markedly in ease of processing and the percentages of copper yielded. In order of copper content, those commonly exploited are shown below, in blue for the oxides, yellow for the sulphides:
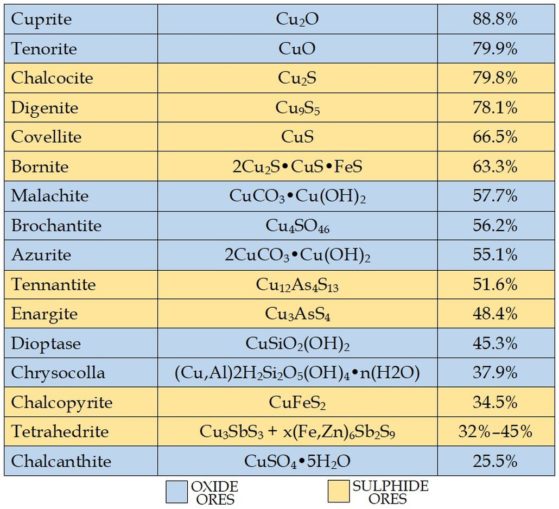
SharpieType301, 2023
OK, that’s all well and interesting, but once you have your copper extracted from the ores, what’s it actually used for?
Copper is the modern world’s third most commonly used metal (only iron and aluminium beat it), and it really does find a considerable number of applications, although not always necessarily as pure copper. Very often, it is used in alloy form, of which there are an enormous number.
Those ‘coppers’, the 1ps and 2ps in your change are alloys. They used to be 97% copper, but since 1992 they’ve been 94% mild steel, with only 6% copper. Progress, eh. Actually, precious few copper coins are now minted, and, with current rising prices, they’ve become near worthless so they may not be around for much longer.
In jewellery, copper is an important component of ‘gold’, which is too soft to be used as a pure element. Your 18K yellow gold ring is actually an alloy containing 12.5% copper, 22.25% copper if it’s rose gold. Being a spark-free, non-magnetic metal, as well as corrosion resistant, it’s also used in a number of small-scale mechanical devices. These include clocks, watches, and timers, typically in springs, balance wheels and hands, or as bronze for bearings. That spark-free property comes into its own in situations where there is a significant concern about explosions. Tools made from beryllium-copper or aluminium-bronze are recommended in these circumstances. These tools (e.g. axes, hammers, pliers, and screwdrivers, etc.) are also non-magnetic and corrosion resistant.
The brass section of a band wouldn’t exist without copper. Brass is another copper alloy, and is used to produce horns, trombones, trumpets, and saxophones. For that matter, electric guitars wouldn’t work without copper – it’s in the wiring, connectors, pick-ups, and the strings. The percussion section needs it too, and copper-based metals are used for instruments such as cymbals and, wait for it… some triangles.
Speaking of ‘instruments’, instruments of war, that is, bronze (which is a copper alloy) was long the preferred metal for naval cannons. Even though the famous Tudor carrack-type warship ‘Mary Rose’ (sunk in 1545, during the reign of Henry VIII) carried a mixture of bronze and iron ordnance, this all changed during the reign of Queen Elizabeth I. Her Navy was to be entirely equipped with cast bronze guns, and by 1569, these were the norm.
Though more costly to purchase than iron, bronze is easier to cast (in addition, if damaged, it can be recycled and re-cast). It is stronger than iron and withstands the shock of discharge better. Furthermore, its resistance to corrosion means it weathers the marine environment better, so the weaponry lasted longer. Although now superseded, another copper alloy, gunmetal (a type of bronze), was common in days gone by. As the name suggests, originally this was chiefly used for making guns and ordnance.
In building and construction, copper (and various alloys) can be found in building fascias, roofing systems, gutters and downpipes, cladding, flashings and copings, and expansion joints. It’s frequently seen on domes, and spires, and an assortment of other architectural features. An extremely common use is for plumbing pipes and fittings, water tanks, gas pipes, and other general engineering applications. Of course, copper will feature in almost all of the electrical cabling and associated electronic bits and bobs a modern house requires. Indeed, an average home will contain something in the region of 400 lbs of copper.
But it’s not only used in a building related setting, but also in transport. Copper is used in cars, trains, overground and underground, trams, and buses. Copper is used in wiring, and circuit boards, in transformers, and general electronics for all sizes of motor vehicle (typically a ‘standard’ car will contain c.50 lbs of copper, of which around 40 lbs is in electrical components).
In examples old and new, the 1921 Rolls Royce Silver Ghost had a body which was entirely manufactured from copper, engine hardware of solid brass, and a radiator made of copper and brass. Looking to the modern day, the Tesla Roadster is powered by an electric motor powered by a copper rotor, the first commercially available EV car to use this technology. Copper is also added to lubricants, helping to make vehicle engines run smoother and last longer.
It’s found in the skies too, where it has long been an important aviation material. Aircraft engineering makes use of copper, not just in wiring looms, but for a variety of other purposes. Aluminium-copper alloys are used in aircraft construction, since the copper increases the strength of the material. As an example of the need for copper, a plane we’ll all be pretty familiar with, the Boeing 747, included 4,000 kg of copper, some 2% of its overall weight. That included a whopping 632,000 feet of copper wire.
A number of copper-based alloys have been developed especially for aviation, particularly for systems where safety‐critical components are required to be reliable over the long‐term. The alloys provide trusted materials with high strength, good malleability and ductility, and resistance to corrosion. New applications are still being dreamed up. To provide part of the lightning protection system for the Boeing 787 Dreamliner, copper mesh is embedded in its composite skin.
But let’s not leave out water transport. As far back as the 1760s, copper sheathing was used on British Navy ships to protect the wooden hull from teredo (a.k.a. shipworm, which devour ship’s timbers from the inside out), barnacles, and other marine pests, making their ships faster and more manoeuvrable. The first vessel to get this treatment was the frigate HMS Alarm. This practice spread through the Navy (indeed, Admiral Augustus Keppel remarked that coppering ‘gave additional strength to the Navy’). This sheathing was also adopted by the East India Company. In fact, by 1786, nearly three hundred commercial vessels registered on the Lloyds of London list were described as ‘copper-bottomed’. This phrase became associated with a ‘reduced risk’ and remains in use to this day.
Of course, the tonnage of pure copper needed to protect a ship’s hull was expensive, so it wasn’t long before an alternative was developed. The Birmingham industrialist George Frederick Muntz developed a copper-based brass alloy (Muntz metal, 60% copper, 40% zinc, with a trace of iron) in 1832 as a replacement. This was produced at Smethwick’s French Wall’s iron works and did the job admirably. Furthermore, the cost of this material came in at around two thirds of the price for copper. Unsurprisingly, this was quite a success, so Muntz made a considerable fortune. As late as WW2, almost all small Admiralty vessels operating in warm waters were sheathed in Muntz metal, which was laid on a base of tarred felt. A copper-based alloy is still used for this reason, even in modern sea vessels. Again, to bring things closer to the present day, about 200,000 pounds of copper was incorporated into Triton-class nuclear submarines.
Copper finds a role in a range of other industries too. It’s been estimated that in large North Sea and Baltic offshore wind farms, each turbine will contain around 33 tons of copper in windings which make up the ring generators alone. It’s also found in the high-voltage and low-voltage power cables and is vital to the electrical grounding systems (to provide protection from lightning strikes). Given that these offshore wind turbines are surrounded by seawater, being pretty resistant to corrosion makes copper even more valuable.
That very corrosion resistance finds a use in another industry. The containers in which nuclear waste is buried are encased in a heavy (several inches thick) copper shell by some countries. Copper’s resistance to corrosion means these containers can be deemed ‘safely’ buried for several hundred thousand years.
Because it is such an excellent thermal conductor, copper is used in cookware, heat exchangers, car and vehicle radiators, and heat sink components. Your beer wouldn’t stay cool without copper, as it’s a vital component of your fridge and freezer.
Oh, and those jeans you’re wearing. The zip holding them up is likely to be copper alloy. It really is an incredibly versatile element.
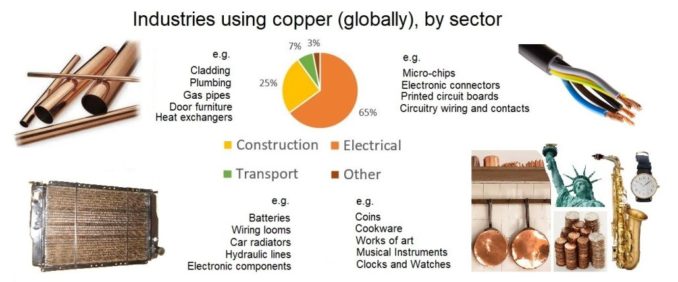
SharpieType301, 2023
Copper ores can be found worldwide and are mined in many countries. Chile holds the world’s largest copper reserves, with an estimated 209 million tons (T) as of 2022. This far outstrips any of the other top five producers, Australia (with 102 million T), Peru (85 million T), Russia (68 million T) and Mexico (58 million T), according to the US Geological Survey.
In the order of 24 million tons of copper are mined globally, every year, and Chile, Mexico, and Peru are home to fifteen of the world’s top twenty largest copper mines. They account for something like 36% of global copper production. Of these, Chile’s Escondida mine, in the Atacama Desert (which also produces gold and silver), is by far the largest. It’s a vast open pit mine with a capacity of 1.54 million tons of copper p.a., more than both the second and third-largest mines (Chile’s Collahuasi and Mexico’s Buenavista del Cobre) combined.
Think about this level of annual production (24 million tons annually and rising) then also consider that copper can be easily recycled, melted down for reuse, and used many times over. In fact, it’s estimated that c. 80-95% of all copper ever mined is still in circulation, being reused. All in all, that’s one helluva lot of copper, which gives an idea of how important this metal is. Even given that, it still ranks third in relation to production volumes amongst metals (again, iron, and aluminium beat it).
But South America wasn’t always the world’s largest producer. Between 1770 and 1805, Great Britain was the largest producer of copper in the world. Exploiting this rich resource came at the perfect time for developing industry as the Industrial Revolution had only recently got underway.
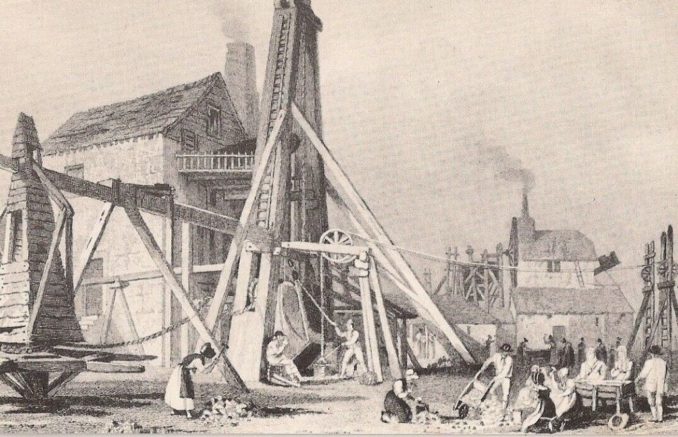
Mark Crombie, Public Domain
Copper mining in Britain had begun considerably earlier, back in the Bronze Age if not earlier. At that point mines on the Great Orme, in North Wales, (now declared ‘the largest prehistoric copper mines in the world’) were the primary source of copper. They remained so for some two centuries, and the copper mined there was traded widely, from Brittany to the Baltic. During the Roman occupation of Britain (around two-thousand years later), copper was still being extracted at the Pen-y-gogarth (Great Orme) mine, and copper from here and mineral resources from Cornwall, including copper and tin, were shipped across Gaul to Marseilles.
By the late 18th century, the main copper producing areas had swapped places, with Cornwall producing by far the greatest quantities, and North Wales (including the Parys copper mine on Anglesey) and Ireland next largest producers. By the late 1780s, British production was well over 8,000 tons per year, and rising, a colossal amount at the time. This came from areas already noted, but also from Ecton, to the east of Leek, in Staffordshire, and a number of smaller mines, mostly in Shropshire.
But the richest copper producing area in Cornwall at that time (18th to early 19th centuries), in fact in the world, was Gwennap. Indeed, between the copper and tin produced in that small part of Britain, it was known as ‘the richest square mile on Earth’. Interestingly, new deposits of high-grade copper ores have recently been found in a previously unmined area, and this may herald a renaissance for copper mining in Cornwall.
But other riches come from this area too. With the boom in mining (both copper and tin, but also zinc, silver, and arsenic), the magnificent Cornish Pasty developed.
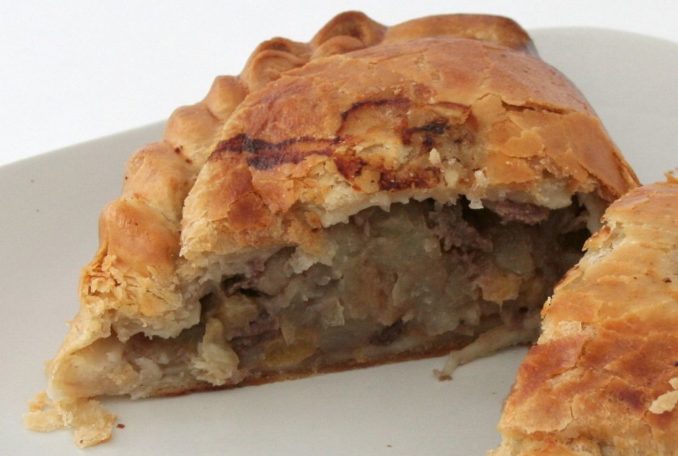
David Johnson, licensed under CC BY-SA 3.0
The ‘Oggy’, as it was known, provided a filling, all-in-one meal of potato, swede, and onion, with whatever meat was available (if any), all in a sturdy pastry case. It gave much needed sustenance for the hard-working copper (and other metals) miners, toiling in extremely challenging conditions. Not for nothing were the Cornish considered the best hard rock miners in the world. The pasty could be eaten down in the mine—no need to come to the surface, and no requirement for cutlery, as that substantial ‘D-shaped’ crust served as a handle. This allowed the miners to hold their meal with dirty hands, without contaminating their dinner. Given the presence of arsenic in many of the mines, chucking the crust away was a very practical necessity!
OK, while there may be no copper in our beloved oggy, your body does require it. As we’ve seen for elements in previous articles, in trace amounts, copper is essential for life. It is present in all of our body tissues, especially structural tissues such as collagen and elastin. Together with iron, copper enables the body to form red blood cells. As a little aside, mammalian blood is red. This is due to the presence of iron, which helps the red blood cells transport oxygen through the bloodstream. But octopus, lobster, shrimp, and crab all have blood which is blue in colour. This is because copper carries out that oxygen transport role in their blood. Brings a whole new meaning to ‘blue blooded’, eh?
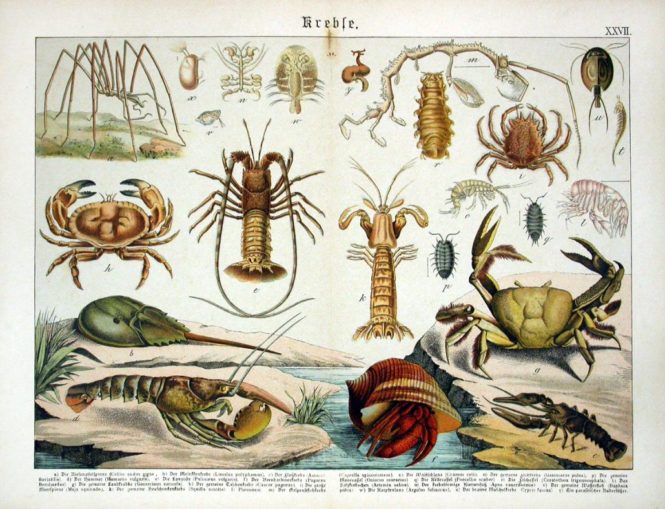
Dolly Blue, Public Domain
Copper plays a role in maintaining nerve cells and the immune system, and a deficiency is linked to a raft of disorders, from cardiovascular to neurological, osteoporosis to arthritis, thyroid function to an increased risk of infection. However, it is found in a range of foods (e.g. organ meats, such as kidneys and liver, shellfish, beans, nuts and seeds, whole grains, dark leafy greens, black pepper, and even cocoa) so supplements are very unlikely to be needed. In fact, just the fact that our tap water largely travels through copper pipes, provides a good amount of the copper we need daily.
It appears that it isn’t only humans who benefit from copper. It seems fish and crustaceans do too, and a trace amount of copper is essential to both marine and freshwater aquatic life. Fish (research has been carried out on salmon, catfish rainbow trout and carp) grow to a larger size if they are in waters with a reasonable copper content, or if fed trace amounts of the element. In part, this effect may be due to the protective aspects of copper in the waters, preventing an increase in harmful microorganisms (e.g. bacteria or fungi) which might impact the fish. But copper is also a key component in the food chain, and an adequate supply is necessary for all aspects of normal metabolism.
With the advent of copper-bottoming, we’ve already seen that our element possesses first-rate anti-fouling properties. Copper has noteworthy bactericidal properties and is known to slow the growth of harmful bacteria such as Escherichia coli, Methicillin-resistant Staphylococcus aureus (MRSA), and Legionella pneumophila. We’ve already seen that many domestic water pipes are made of copper. However, some modern cheap ones are plastic, a trend which seems to be rising. This might seem a practical, economically sensible way forward, until you consider that, in copper pipes, bacteria multiply about 100 times slower.
It’s antimicrobial properties, (along with the ease of shaping, good thermal conductivity, and corrosion resistance), made it an ideal for use in cooking pots, but also in brewing vessels, ‘kettles’, to brew traditional beers. Indeed, these vessels have long been referred to as ‘coppers’ and many such vessels have been in constant use for a century or more. Sadly, primarily for cost reasons, but also because it is easier to clean, in the large-scale breweries copper has now been largely replaced by stainless steel.
Copper has a long history of being used medicinally too, dating back thousands of years. Egyptian medical texts from 2,600-2,200 BC record the use of copper to sterilise chest wounds and purify drinking water. The Roman philosopher Pliny, writing in the first century AD described a number of remedies involving copper, for example using ‘black copper oxide’ (CuO) mixed with honey to eliminate intestinal worms and treat other disorders. In Ayurvedic medicine, copper vessels are used to sterilise drinking water, but drinking the water from these is also said to balance the three doshas – vata, kapha and pitta. In addition, copper bracelets are worn to help with joint or skin inflammation and pain. Even today, copper is still used to treat ailments such as arthritis and skin conditions.
It finds other essential roles in modern medicine too. MRI scanners rely on copper-based superconductors to create the detailed images of the human body. Moreover, since bacteria in direct contact with a copper surface can’t survive for long (it ruptures the cell membrane, killing them before they can replicate to cause an infection) it is being used more in hospital hardware. For this reason, copper or its alloys are becoming more commonly used for frequently touched surfaces in a medical setting, to reduce the likelihood of hospital-acquired infections spreading. In addition, using a copper coating on a modified surgeon’s scalpel can allow electrical conductivity to heat the blade. This means a scalpel can be used to cauterise as it cuts, helping to control blood loss during operations.
This electrical conductivity may bring benefits in the garden too. Copper is a useful slug repellent. It’s thought that this works because the positively charged ions in copper react with water and the protein-based slime with which slugs and snails are covered. This causes an electro-neural effect which, to the unfortunate creatures, probably feels like an electric shock. Hence, they steer clear of your precious plants.
Ah yes, copper, and electrical conductivity. This was something we explored briefly in the previous article, when we considered Alessandro Volta’s work on creating an early battery, his ‘voltaic pile’. Volta developed this in 1799. Might it surprise you, then, to think that someone could have stolen a march on poor old Volta? Almost a 2,000-year march?
Well, the ‘Baghdad Battery’, also known as the ‘Parthian Battery’ or the ‘Battery of Babylon’, may or may not be just that—the controversy, or some might say conspiracy theory, is still rumbling on. Either way, it certainly gives us considerable pause for thought.
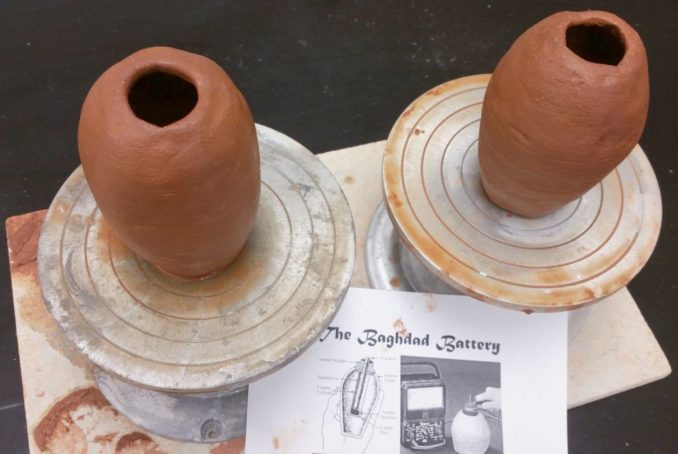
Boynton, licensed under CC BY 2.0
In 1936, a strange object came to the attention of the head of the National Museum of Iraq’s conservation laboratories, an archaeologist and painter called Wilhelm König. This object had been unearthed some four miles north of Baghdad, in a burial at a site called Khujut Rabu’a. The find was an unglazed ovoid ceramic jar with a rough opening at the top, as if a neck had been broken away. Inside the jar was a cylinder made from a sheet of rolled copper with a ‘base’ of the same material, and an extremely corroded iron rod, pointed at one end. There were traces of bitumen, both at the base of the jar and around the neck, which probably acted as a seal.
König was intrigued by this object and suggested that if an electrolyte were added to the interior (something like lemon juice or wine) this vessel could function as galvanic cells, an ancient electric battery. He believed that such a device could have been used to electroplate other objects, possibly with gold or silver leaf.
There were a few difficulties with this explanation, not least of which is that there wasn’t actually any apparent way to connect wires to the copper and iron components. Add to that the other effective techniques to gild objects which were already known to the ancients—why would the Parthians need this one? Furthermore, there is a distinct lack of any written evidence, or even intimations, about similar devices. But hey, let’s not let that get in the way of a good ‘Indiana Jones’ style story.
Dr Brad Hafford, from the University of Pennsylvania, gives a great overview of this object (and similar ones from Iraq), plus the proposition which stemmed from König but which has perpetuated ever since, in his video ‘The Baghdad Battery? Archaeologist Reacts!’. I’ll leave it to you to decide what you think.
I’ll leave you with one final snippet related to our element, or at least one which shares its name. This is one of the (very many) slang terms for a police officer. Er…, no, I’m not referring to any of those fond terms used here.
The term ‘copper’ as slang name for policeman comes from the mid- to late-1800s (our Vol. 1 of the 1933 Shorter Oxford English Dictionary suggests it dates to 1859, though it’s said to have first been seen in print in 1846). Various theories about the origin have been proposed, one of which is that the early uniforms would have had copper buttons. Others theorise that is relates to ‘Constable on Patrol’, which to my mind rather misses the point.
More likely is that ‘copper’ derives from the Latin word ‘capere’, which means ‘to seize’. That said, it seems to have morphed through a number of different languages (e.g. Dutch ‘kapen’ or French ‘caper’ to take) to give us our ‘copper’. This Latin word is the same root as that for out English word ‘capture’.
Interestingly, the term ‘copper’ was first used by the criminal fraternity for a street thief (the inference here is an individual who ‘seizes’ another person’s property!). When arrested, the ne’er-do-wells were said to have been ‘copped’ and the officers doing the ’copping’ therefore became the ‘coppers’.
In practice, does this have a darn thing to do with our element? Well, no, it doesn’t really, but it does provide an opportunity to reminisce about a TV programme that I, and many of you, will remember with a great deal of childhood pleasure. Oh, and join George Dixon (Jack Warner), in using his quintessential catchphrase…
Adapted from Leonard Bentley, licensed under CC BY-SA 2.0
© SharpieType301 2023