In a previous article, I asked whether you had ever gazed into your pint and wondered about the beginnings of beer and brewing. This time, I’ll ask you another question. It’s about the pint pot sitting in front of you, the one you are probably taking for granted.
What’s so special about it? Surely, it’s just a thing. OK, it’s a useful thing, but its only purpose is to raise that gently foaming golden liquid to your eagerly waiting lips. Just a common or garden, utilitarian item… or is it?
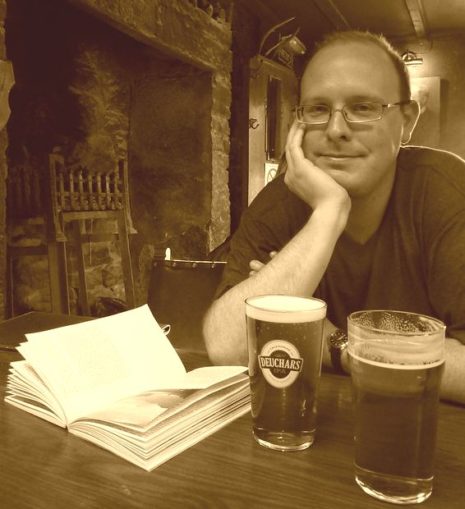
Casual pub contemplation, Andrew Bowden – Licence CC BY-SA 2.0
Cropped and sepia toned from original.
Well, the concept of functionality is accurate, but that pint glass has a fascinating history. Both the glass itself, and the material from which it has been made, so let’s take a closer look.
The earliest drinking vessels would not have been made from glass, which was a material for society’s elite—far removed from the common people. Drinking cups would have been practical, sturdy and able to withstand a few knocks. If possible they’d be repairable, so they could be quite long-lasting. They’d sometimes be home-made, but more often made by local craftsman. They’d have used plentiful and cheap materials, such as wood (possibly staved, like a barrel, or block-carved), or horn (typically cattle). Others, for the better off, might be metal or pottery.
Tankards were also made of leather. This was ‘worked’ when wet so it became flexible, then shaped and finally waterproofed with beeswax, birch sap, pitch or tar. These were called ‘jacks’ or ‘blackjacks’ and were very common during the 17th Century. In fact, their use continued right up to Nelson’s time when they were known as ‘boots’. Hence the naval exhortation to ‘Fill Yer Boots’.
Right up until the end of Victorian times, ale in pubs was usually supped from durable pewter or ceramic (commonly china or stoneware) tankards. Robust yes, but they had another advantage. Being opaque, they nicely hid any unsightly sediment floating about in the beer and gave an opportunity to unscrupulous innkeepers to short-change their customers!
Tankard with hunting scene… by Daderot and Quart Mug MET 132005 by Joseph Danforth, both used under CC0 1.0, Combined and annotated.
But, as filtration techniques were introduced to produce clearer, brighter beers, and as formerly dreary inns, taverns and alehouses acquired better light (with the advent of gas lighting replacing oil lamps and candles), beer served in glass gradually started to come to prominence. No longer a luxury item, the mass production of suitable glasses allowed the colour and clarity of the contents to be admired, adding to the enjoyment of the ales and ensuring the pint you paid for was a full measure!
Beer Samplers bycodepo8 is licensed under CC BY 2.0
Before I go into more detail about beer glasses, as is my wont, I’m going to head off at a tangent for a while and look a little more closely at the glass itself. What is it and where did this material, now something we use every day without paying much attention, come from?
Where did glass come from?
Perhaps surprisingly, the earliest glass used by man wasn’t man-made at all. Long before metals were available, Neolithic (Stone Age) societies needed sharp points and cutting edges for a wide variety of tasks. They made use of certain types of brittle stone, such as flint or chert. Because these break with what are called ‘conchoidal fractures’ when struck with sufficient force, thin, sharp slivers or splinters, usually referred to as ‘flakes’ or ‘blades’ can be formed. This is known as ‘knapping’. However, not only stone was used in this way. Glass, or glassy substances, can form naturally, and can also be knapped.
Obsidian is probably the best known. A hard, brittle, naturally occurring volcanic glass, usually black (although it can also be green, brown, red, blue, yellow, or orange), obsidian can form when lava cools rapidly. Like flint and chert, it fractures conchoidally to create fragments with wickedly sharp edges. It could easily be used to make cutting and piercing tools. But, being volcanic, it is not ubiquitous, so this rare and useful material was highly valued and widely traded.
A related material is ‘impactite’. Impactites are natural glasses formed by the impact of a meteorite. Libyan Desert glass (sometimes called Great Sand Sea glass) is one example, and this is known to have been used by Neolithic people to make tools. Another form of natural glass is ‘fulgarite’ which is formed by lightning strikes, though I am not aware of this being used by early man.
Despite natural glasses being used by early man though, glass is typically envisaged as a manufactured material. Yet there is still some uncertainty about where the first glass was made. To date, the first archaeological evidence for man-made glass comes from Eastern Mesopotamia, but the techniques developed there appear to have been introduced to Egypt and Syria shortly afterwards.
Yes, the origins of glassmaking come from same region I mentioned in a previous article—the birthplace of beer. Brewing, at some 13,000 years ago, pre-dates glassmaking by quite a wide margin though. However, the first evidence of glass that has been found wasn’t anything to do with drinking vessels. Quite different, it was in the form of non-transparent beads, dating to around 3,500 BC. Vessels made of glass only made an appearance during the reign of Pharaoh Thutmose III, 18th dynasty Egypt, around 1,450 BC.
In fact, these very early ‘glass’ beads were not quite glass as we know it, but a closely related material called faience. Faience is sometimes described as ‘finely glazed ceramic’, but it isn’t actually pottery at all as it contains no clay. It is instead a vitreous, glassy frit, a polycrystalline material where a solid mass of material is created by ‘sintering’ either by heating it, but not to its melting point, or by the application of pressure (think of squeezing loose snow together to create a solid, hard snowball). Somewhat later, true glass beads (rather than faience) were made by winding molten glass around a core.
Roman historian Pliny the Elder (Gaius Plinius Secundus, AD 23-79) places the discovery of glass (well, the recognition of its existence) in Syria. Rather quixotically, he relates that it was a serendipitous discovery made by Phoenician merchants transporting stone. He wrote in his Naturalis Historia that:
“There is a story that once a ship belonging to some traders in natural soda put in here and that they scattered along the shore to prepare a meal. Since, however, no stones suitable for supporting their cauldrons were forthcoming, they rested them on lumps of soda from their cargo. When these became heated and completely mingled with the sand on the beach a strange translucent liquid flowed forth in streams; and this, it is said, was the origin of glass.”
Evidence for trade in this prized manufactured material can be identified slightly later, from around 2,000 BC. While the raw ingredients were inexpensive, the glassmaking process requires skilled firing at very high temperatures, so the trade was in unprocessed material (feedstock if you like), destined for manufacture into a finished article at its destination.
Analysis of the chemical composition, particularly trace elements, of the glass used in beads found at Mycenaean Greek sites, dating to between 1,600 BC and 1,100 BC, shows them to have been produced from raw glass imported from both Egypt and Mesopotamia.
It is thought that the renowned Uluburun shipwreck, which has been dated to around the end of the 14th century BC (around 1,300 BC), could have been en route to one of the Mycenaean palaces in mainland Greece. It sank while carrying 175 raw glass ingots as just one small part of its mixed cargo. These were discoid in shape, with rounded bases (not too dissimilar to ice hockey pucks, but larger at around 6” diameter). As the ingots recovered from the wreck were turquoise, deep blue, lavender, purple and amber colours, perhaps they were destined to become beads.
What is glass?
Most of us recognise glass when we see it but, essentially, man-made glass is created from sand. Chemically, this is silicon dioxide (SiO2, also known as silica or quartz). Not every type of sand can be used, but sand collected from inland continental deposits or non-tropical coastal areas is usually the most suitable.
For the next bit, imagine that the sand is sugar—this isn’t quite as daft as it might sound. On TV and film sets the ‘windows’ are in fact made from sugar, which looks just like glass, but won’t rip the stuntmen (or women) to pieces as they dive through it!
IMG_3070.CR2 by dido is licensed under CC BY 2.0
Common or garden sugar is small and granular (analogous to sand). When you heat sugar it melts (transforming from solid granules to a liquid form).Then, once the heat source is removed and it cools, it returns to a solid form—it’s still sugar, but it’s no longer granular. Instead, you now have a hard, brittle ‘toffee’ or ‘candy’, usually transparent or at least quite translucent.
When granular siliceous sand is heated it behaves in a remarkably similar way, melting, then cooling to give silica glass. It isn’t simple to produce though, as pure siliceous sand requires very high temperatures to melt, typically over 1700° C (> 3090° F).
Pure, clear, transparent glass wasn’t achievable in ancient times, not only due to the temperatures required but because, as collected, sand almost inevitably contains a variety of minerals and other impurities which can affect the appearance of the end-product. However, that’s not all bad as these impurities often lower the melting point.
Modern ‘pure’ silica glass has specific properties which render it useful for a range of technological applications. Silica glass has very high resistance to thermal shock, it is chemically inert (so has excellent chemical resistance), has very low electrical conductivity, and good ultraviolet transparency. It is commonly used in high-temperature lamp envelopes, lenses and mirrors where temperatures are highly variable, components of laboratory analytical equipment, in microwaves, and for aeronautical radar windows.
On the other hand, the type of glass we generally see in windows, jars and bottles is not silica glass, but a variation called soda-lime glass. Rather than just melting a single ingredient, this combines silicon dioxide (SiO2) with sodium oxide (Na2O) and calcium oxide (CaO), a.k.a. lime. There can also be other additives and, depending on the proportions of the mixture of materials, the properties of the glass produced will vary. Certain additives are used to deliberately lower the melting point or change the viscosity (making it easier and/or cheaper to produce), some will alter other physical properties of the glass. Specific additives, typically metal oxides, can give what is normally relatively colourless glass a colour, but more on this in a moment.
The fact that glass can be melted to change its form (without destroying its components) means that glass can be recycled time and again. Without doubt, the Doom Goblin must love this stuff. The cycle is melt à make à use à break up à re-melt à re-use. Re-use can be for the same or a completely different product, e.g. glass bottles and jars recycled to use in industry as aggregate (building material).
When you look up a description, glass is defined as a “hard, typically transparent, material” or as a “non-crystalline, amorphous solid”.
OK, so what does that mean?
Based on their micro-structure, there are three main forms of material: crystalline; polycrystalline; and non-crystalline.
Crystalline solids are materials where the constituent parts, e.g. atoms, molecules, or ions, are found in a regular, repeating arrangement to give a highly ordered, symmetrical microscopic structure. Single crystals have a distinct geometric form, with facets (flat faces) which lie in a specific orientation common to all crystals of that material. This means adjoining crystals of the same material will stack perfectly in three dimensions, leaving no gaps. Examples include diamonds, where atoms of the element carbon are arranged in a cubic structure, and common salt, again arranged in a cubic structure, but this time with atoms of two different elements, sodium [Na] and chlorine [Cl], making up an ionic compound, the molecule sodium chloride [NaCl], which is held together by electrostatic forces.
Polycrystalline materials are made up of numerous microscopically small crystals, called crystallites or ‘grains’. Some regions of these crystallites line up neatly, but other sections lie in different orientations, not symmetrical so the boundaries between them are imperfect. They can’t stack seamlessly in three dimensions throughout the entire material, so some gaps are left. Where this happens, the spaces may be filled with amorphous material, holding the crystallites together. Typically, ceramics and metals are polycrystalline, as is ice.
Non-crystalline materials, sometimes described as amorphous, vitreous, or glassy, don’t have any form of ordered structure. They are still made up of interconnected ‘blocks’ of material, but these are not arranged in a regular, regimented pattern. In fact they can be quite chaotic, so cannot stack neatly in three dimensions without gaps. In addition, depending on the strength of the links between these ‘blocks’, the material formed can be liquid (low-strength links) or solid (high-strength links). Gels, thin films, polymers and, of course, glass, are amorphous materials.
Structural differences © SharpieType301 2020
Glass and colour
Where a completely clear, transparent glass is required, pure white silica sand, usually tiny weathered pieces of quartz, with particularly low inclusion levels is chosen. This type of quartz silica sand is most commonly, but not always, found in deserts.
As I mentioned when we looked at what glass is, depending on the geographical source of the sand, there are likely to be mineral inclusions along with the silica grains. Minerals found in sand from different locations can lend a variety of distinct colours to the glass, with perhaps the most common inclusions resulting in a green or brown tinge. Early glass, as we have seen, was not clear and transparent (not until 9th century BC were techniques for producing colourless glass developed, in Syria) but it was often coloured due to the impurities in the sand used to make up the glass mixture.
00065 sand collage by Siim Sepp, licensed under CC BY-SA 3.0, WhitehavenBeachSand01 by Noah Unsworth, licensed under CC BY-SA 2.0 and Sand Penny by Paul VanDerWerf, licensed under CC BY 2.0, Images cropped.
But to deliberately colour glass, small quantities of pure metals or metal oxides are added to the mixture of ingredients. Different metals give different colours. This can be done before the mix is heated, after the mixture has melted, or the metals can be applied to the surface of hot glass. Colouring glass may have been an accidental discovery at first, but people have always been remarkably resourceful, so early glass-makers learned to deliberately add various minerals to glass. This idea was rapidly adopted and has been around for a surprisingly long time.
Some of the earliest Egyptian glass was crafted in a variety of vivid colours. Glass was regarded as an artificial semi-precious stone, and the Egyptians produced glass in various colours to mimic different gems. Coloured glass was often used for small bottles, vases, and bowls, many of which were made to hold cosmetics and sweet-smelling unguents.
Cosmetics jar by Tim Evanson, licensed under CC BY-SA 2.0
They produced milky-white glass using tin or lead oxide (possibly emulating pearls), they used copper or iron compounds to give a greenish-blue (imitating the highly prized gemstone ‘turquoise’), and cobalt compounds to produce a deep blue (emulating the valuable semi-precious stone ‘lapis lazuli’).
Copper oxides gave them red and orange glass. Manganese could be added to the mix in quite high concentrations to produce an amethyst or violet coloured glass. Lead or antimony gave them yellow glass, and black glass could be formed by using a large amount of copper and manganese, or with ferric (iron III) compounds.
In more recent times, other metals have been used to make coloured glass.
Take red glass. For a rich ruby-red, a tiny amount of gold can be added, and for a cranberry-red glass you’d reduce that small amount of gold to an even tinier quantity. Copper, as a pure metal, produces a very dark red glass, but this is opaque so is less often used. And, for particularly bright red glass selenium is used, added along with cadmium sulphide.
The rich green glass of wine bottles owes its colour to the addition of ferrous (iron II) oxide and chromium. Adding nickel to glass ingredients, at different concentrations, gives blue, violet, or black glass.
The milky white opaque glass (sometimes called opal or opalescent glass) can be made, as we’ve seen from the Egyptians, using tin dioxide and arsenic and antimony compounds. Glass from the Tiffany Studios in New York (founded by Louis Comfort Tiffany) used this to create their iconic styles, incorporating marbled, mottled or streaked glass.
For yellow glass, silver compounds (especially silver nitrate) can be added, and if the mix includes both cadmium and sulphur, a deep yellow colour can be achieved. Another element that’s been used to produce yellow glass is uranium. Although a radioactive element, the uranium is added in very small amounts, so the resulting glass is not dangerously radioactive. Just as well, as I plan to drink champagne from our beautiful, Thomas Webb, engraved champagne saucers one day.
Uranium glass champagne saucers © SharpieType301 2015 (photographer Tom Mayle)
Methods of decoration
Glass is incredibly versatile and can be decorated or enhanced in a variety of different ways.
Using colour is an obvious way to decorate glass objects, and patterns can be formed by combining coloured glass using various methods to enhance an object’s appearance.
Mosaic uses small pieces of coloured glass (as well as stones and shell) to create complex and luxurious designs and pictures. This is commonly seen on floors but was also used as wall decoration. Indeed, this technique can perhaps be regarded as the earliest form of pointillism, pre-dating Georges Seurat and Paul Signac by millennia.
Millefiori is a technique where colourful patterns are produced by heating a bundle of thin glass rods of different colours until the rods fuse together. Although this is now thought of as an Italian technique (as they coined the name, which means ‘a thousand flowers’), it was developed by the ancient Egyptians, being first known from Alexandria and dating to the 2nd century BC. The fused bundle of assorted coloured glass can be stretched and pulled thin or folded back on itself to form different patterns. Then once cooled it can be sliced across the length, producing small disks with a distinctive design that doesn’t change along the length of the bundle (very much like a stick of seaside rock). The cut disks can be pressed onto hot glass, for example a vase or bowl, and reheated to fuse the two.
Cameo glass combines he use of colour and carving in a highly complex technique to create wonderfully decorated objects. Made to mimic naturally layered gemstones such as agate and onyx which were carved to make jewellery, multi-layered glass ‘blanks’ are created, ‘casing’ or fusing two or more layers of differently coloured glass. These often comprise a dark inner glass layer with a white or lighter coloured outer layer or layers. By etching and/or carving through the fused layers of differently coloured glass, meticulously detailed 3D designs can be created (similar in appearance to, and in fact copied by, Wedgwood jasperware). One of the finest cameo glass artists in the world today is Helen Millard. Her work is stunning, as she blows her own multi-layered blanks and then engraves them, to give her complete control over the entire process.
Helen Millard cameo glass bowl © SharpieType301 2015 (photographer Tom Mayle)
Coloured glass is also at the heart of the stained-glass windows we are all familiar with. In these, small pieces of coloured flat glass are cut, then assembled to form patterns or pictures. The pieces are held together in lead ‘cames’ (‘U’-shaped strips) and the whole design supported in a rigid frame. More detail can be added by painting colour onto clear glass (e.g. using silver stain to give a range of yellows and gold) or by painting onto coloured glass with another colour (e.g. white, black or brown glass paint). Enamelled glass (where powdered coloured glass, usually mixed with a binder, is painted onto the surface, then fused to it in a kiln) was another common decorative method.
Stained and painted glass © SharpieType301 2014
Shape offers another decorative element to glass objects. One of the earliest manufacturing techniques for small vessels was core-formed glass. This originated around 1,600 BC, and objects were made by creating a ‘core’ in the rough shape of the interior of the bottle, vase, etc. Commonly a combination of clay, sand, mud and/or animal dung, the core was shaped around a rod. Molten glass could then be trailed onto the core. Alternatively, the core could be dipped into a container of molten glass. The surface could be smoothed by ‘marvering’, re-heating and rolling the glass (still held on the core) across a flat slab. A base, feet, handles and a rim could be added at this stage. Once cooled, the rod would be removed, and the core material scraped out. Only small vessels, with thick walls, could be made in this way. But they could be highly decorative—common body colours were cobalt blue, opaque white, brown, red or olive-green and the decoration often opaque yellow, orange, white or turquoise trails in zigzag or feather patterns. These were opulent items, available only to the wealthy.
Around 1,200 BC the Egyptians learned how to press or cast glass, forming the required shape by placing a blob of molten glass into shallow, open moulds. Rather later glass was pressed into moulds with a plunger or “follower” to form a more defined interior shape. Moulding used a variation of soda glass which was particularly pliant or ductile. Progress indeed, and although these types of glassware tend to be quite thick and heavy, they were still only available to society’s most affluent members.
It was not until the 1st century BC that Syrian glassworkers (in the region around Sidon, Aleppo, Hama, and Palmyra) made a simple discovery. They found that if cool air is blown into molten glass, it will start to inflate. Thus, glassblowing developed, which allowed thinner, lighter, and therefore more economical vessels to be made as much less glass was required. Initially, glass was blown into decorative moulds—still high-class and luxurious, these vessels were commonly shaped like shells, clusters of grapes, or human heads.
A slightly later development by Syrian glassmakers was ‘free-blowing’ glass, forming vessels without the use of moulds. Semi-molten glass with the consistency of molasses (the ‘metal’) was gathered onto the end of a hollow pipe. The glassmaker then blew down from the other end of the pipe to inflate the hot glass into a bubble. This could then be formed into a vessel by blowing to make the bubble larger, swinging to elongate it, or rolling on a smooth stone or iron surface (‘marvering’) to further shape or smooth the surface. As for core-formed glass, additions, such as stems, feet, or handles, were attached by ‘welding’ on pieces while the glass was still soft, so could be manipulated with hand tools or cut with shears.
Between the 1st and 3rd centuries AD, glassmakers from the Roman empire embraced glassblowing and other sophisticated techniques, developing glassmaking as a large-scale manufacturing industry which resulted in glass becoming established as a commonly available material in the Roman world. Both the quantity and variety of glass vessels available increased dramatically, for both extravagant high-status objects, and more prosaic domestic glass vessels. Strabo commented in his Geographica that:
“a [glass] drinking cup could be bought for a copper coin”
Roman glass made its way across the empire, from Britain and across Europe, to the Parthian Empire (in western Asia), Afghanistan and India and as far as China and the Han dynasty.
Once a glass object is formed, numerous other techniques can then be applied to further decorate and enhance it.
We have already explored colouring techniques, but ‘cold working’ is a collective term for techniques such as engraving and cutting, grinding (abrasion) and polishing, which can be used to alter or decorate glass when it is cold. These are similar techniques—in effect, a small amount of glass is removed from the surface of an object by grinding it with a rotating wheel, sometimes under a continuous stream of water. Increasingly fine-grained wheels can then be used to smooth and polish the surface.
But let’s get back to beer glasses
Most everyday drinking vessels, including those for beer, would have been made from different materials. Indeed, George Orwell described a favourite of his in ‘Moon Under Water’—a humble strawberry-pink English china pint mug with a white strap handle (apparently a common sight until around the end of WWI).
However, drinking beer from glass vessels was known in Britain as early as the mid-1600s. But at that time, merely the elite used glass to sup their beer. Only they could afford the luxury of these costly, one-off, highly decorative, often engraved and personalised status symbols.
1, 4 and 5 Mug MET 69819, Mug MET 56791 and Mug with cover by Metropolitan Museum of Art, licensed under CC0 1.0, 2 and 3 Tankard (AM 1966.253-2) and Mug (AM 10425-1) by Unknown author, licensed under CC BY 4.0 All images cropped and desaturated from originals.
The first mass-produced glass vessels for drinking establishments came along much later. This was in the form of a 10-sided, handled pint mug, sometimes called ‘the lantern’. By Victorian times this was becoming relatively common and by the 1920s it had obliged brewers to improve the clarity and quality of their ales. So ubiquitous was this classic design that it featured in the ‘Beer is Best’ promotional campaign run by The Brewers’ Society from the 1930s right through to the 1950s.
Magazine advert for the ‘Beer is Best’ campaign © SharpieType301 2020
The ‘dimpled’ pint mug arrived on the scene sometime around the late 1930s and, in part, its popularity came from a change in drinking habits. There was a shift away from dark mild brews to the ‘pale ale’ style beers, or bitter. The golden or amber tones of these beers look particularly attractive catching the light in dimpled glasses, whereas the straight-sided ‘lantern’ type mugs better suited the old darker brews.
Other beer glasses commonly seen at that time were tall straight-sided, conical ones. But their design had a flaw as they tended to chip where the rims rubbed together when they were washed and stored. This problem was overcome by the introduction of the ‘Nonik’ (no nick) glass in the late 1940s. The bulge about an inch or so down from the rim, strengthened the glass, made it easier to grip, but also meant that glasses could rub together or be stacked without harm coming to the rim.
- a relaxing evening by Crispin Semmens 2) Half pint tankard by Neil Turner 3)Take Courage by bob walker, licensed under CC BY-SA 2.0and 4)Ya llego la cena by Jose A. Perez5) Fuller’s Honey Dew at The Wharf by Bernt Rostad, licensed under CC BY 2.0 All images cropped from originals.
As well as the traditional shapes, in Britain today there are many different shapes of beer glass. Some, like the ‘tulip’, are practical, others are more of an advertising gimmick. For a truly astonishing variety of different shapes, you only need to cross the English Channel to find stemmed beer glasses, straight ones, pilsner glasses, beer mugs, boots and even beer horns. In particular, the huge numbers of different Belgian beers and ales are served in an equally varied number of different shaped beer glasses. Typically stemmed, these include snifters, tulip glasses, schooners, goblets and chalices.
If you’ve read this far, you’ve probably gone a bit glassy-eyed by now, so another little side-track seems in order.
For hundreds of years, whether served in a glass vessel or not, the alcohol in beer made it safer to drink than water. This made it a common drink for the working man, and our brave boys in blue of old were no exception.
In the early years of Robert Peel’s Metropolitan Police, founded on 29 September 1829, being drunk on duty was by far the main reason for dismissal from the force, as recorded in the Met’s Numerical Registers. Of the first 2,800 new policemen only 600 managed to keep their jobs. The Register shows that nearly all of them were dismissed for being drunk. Mind you, the fact that it was the responsibility of the Peelers to supervise Licensed premises would probably not have helped.
One poor chap, William Atkinson, set an astonishing record. He was the man to whom the Metropolitan Police’s first ever warrant number (No. 1) was issued. He didn’t hold onto that warrant very long though—he was dismissed for being drunk on 29 September 1829, the very first day of the new police force. He’d been in the job for only four hours!
Drinking on Duty by Leonard Bentley, licensed under CC BY-SA 2.0
I recently read an anecdote from an ex-copper whose great grandparents kept a beer house in Bethnal Green. Apparently, it was common to leave the back-yard door unlocked and a couple of pints of beer out for passing constables. It was all rather different by the time he joined the Met, and he mentioned that it makes you wonder what state they’d have been in at the end of their shift if all the pubs and beer houses in the area followed this tradition.
Not that a drop of pop isn’t still consumed now and again. A Freedom of Information request from 2017 showed that 41 officers had been disciplined for being drunk on duty in the previous five years, and a further 138 were involved in ‘alcohol-related incidents’ off duty. However, this is a very small minority in comparison with the days of the Peelers—the police are rather more likely to encounter beer glasses while on duty when a physical attack using a glass as a weapon (a so called ‘glassing’) takes place. Even this is diminishing, as the use of toughened glass in pubs and clubs to prevent such attacks has been encouraged over the last twenty years or so.
A final thought
Now as you sit and gaze into your pint glass, consider what author and self-help guru Stephen Richards had to say about glasses, half full or half empty.
Two-pints-beer-main by U3144362, licensed under CC BY-SA 4.0
©️ SharpieType301 2020
The Goodnight Vienna Audio file